介绍
传统的切片是通过划片刀或激光将硅晶圆最终切割成单个芯片或晶粒的工艺,在半导体工艺流程的最后阶段进行。 划片刀或激光用于沿着被称为切割道的芯片之间的区域切割晶圆。 该步骤将晶粒从晶圆上切下,使其准备好被封装并安装到它们最终将进入的任何设备中。
等离子切割通过使用氟等离子体蚀刻掉芯片之间切割道中的材料的干刻工艺,可以实现相同的结果。 与刀片或激光相比,等离子切割被半导体行业认可为首选解决方案,尤其是在芯片变得更小、更薄和更复杂的情况下。
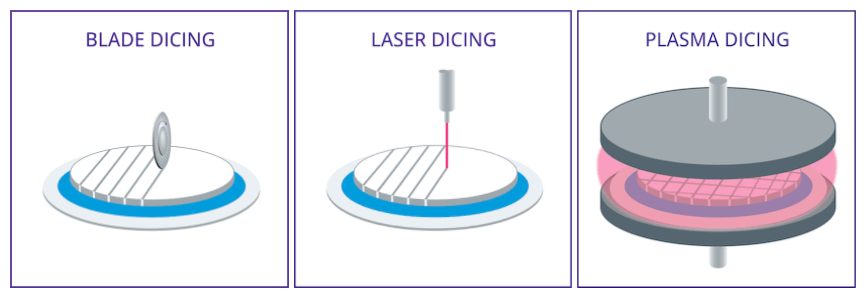
什么是刀片切割?
刀片切割是使用高速旋转的研磨盘(刀片)沿切割道进行切割的工艺。 通常,刀刃由磨料或极薄的金刚石制成,可用于切片,即进行切割或简单地在硅晶圆上开槽。 但是,就像任何机械切割方法一样,刀片切割依赖于物理方式去除材料,这可能导致芯片崩角和崩裂,从而导致产品受损和成品率下降。
什么是激光切割?
顾名思义,激光切割是使用激光技术将晶圆切割成芯片。 该工艺涉及将高功率密度的激光束照射到晶圆上,产生局部高温点以去除芯片之间的切割道区域。 激光将材料加热到某个高温,即激光光斑照射下的区域被吹走(烧蚀)或简单地蒸发。 激光也可以进行聚焦,将热量传递到晶圆的主体内部中,这种方法被称为“隐形”激光切割。 对于这种方法,来自激光的热量会在切割道内产生空隙。 这些弱化区域随后在晶圆拉伸时,通过断裂的方式达到类似穿透的效果。 与刀片切割的方法相比,激光切割的成本要高得多。
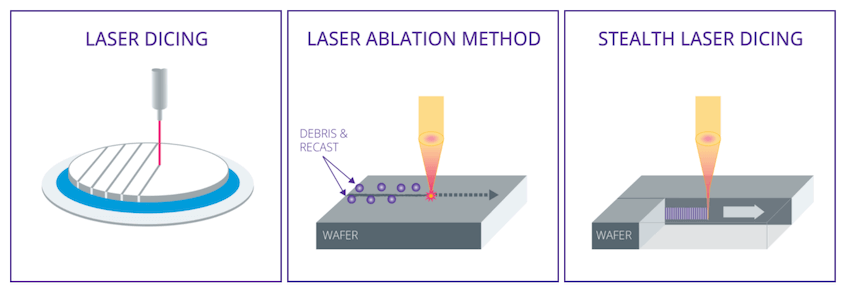
为什么选择等离子切割?
与其他传统切割方法相比,等离子切割具有许多优势。
提高成品率
等离子切割以化学方式去除切割道中的材料。 对芯片没有机械损伤、热影响区或其他物理影响。 这意味着等离子切割不会造成损坏。 与通过刀片或激光方法切割出的晶粒相比,通过等离子切割得到的晶粒具有更高的抗断裂强度。
这种机械完整性的提高,对于在使用中受到物理应力的晶粒来说是一种特别的优势,例如高带宽存储器(HBM)的混合键合堆栈中的应用场景,如果堆栈中的某个晶粒出现故障,则整个设备就会丢失。
随着晶粒朝着更薄的方向发展,以及行业路线图将厚度向低于50µm的尺度推进,等离子切割的非机械特性体现出自身的价值。
提高生产量
刀片切割和激光切割都是沿着切割道逐一进行的“顺次”切割工艺。 特别是对于激光,可能需要多次切割。 等离子切割可以同时“并行”去除所有切割道。 这意味着,随着晶粒尺寸越来越小(即,更多的切割道,因此需要更多次的切割),并且晶圆变得越来越薄(等离子切割需要去除的硅晶圆材料更少,或需要更低的刀片速度/激光功率以避免损坏晶圆),在这些条件的约束下,等离子切割成为了最快速的工艺。
增加单位晶圆可切割晶粒数
在没有任何物理限制(例如,刀片宽度或激光光斑尺寸)的情况下,等离子体可以实现向更窄的切割道移动,从而有可能增加生产线的晶粒产量。 释放以前机械切割方法牺牲的晶圆空间,现在可以分配用于产出更多的合格晶粒。 晶粒数量提升的潜力是巨大的,特别是在考虑生产更小尺寸的晶粒时。
设计灵活性
由于晶圆布局不受线性切片路径需求的限制,等离子切割可以为设备设计人员在基本晶粒形状/尺寸、移除保护环和晶粒/测试组的定位方面,提供更大的灵活性,以更好地利用晶圆面积。
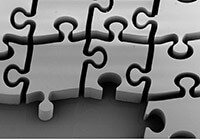
对易碎设备有吸引力
等离子切割对于微机电系统(MEMS)等易碎设备也很有吸引力。 例如,由微小的活动结构组成的惯性传感器,将受益于一种干净的、非机械的切割方法。 不会有物理作用力对晶圆造成振动以及损坏传感功能,也不会有颗粒卡在它们之间并影响其移动。
消除微粒污染物
等离子切割的化学性质仅产生气态副产物,并且可以通过真空抽吸去除,留下干净的晶圆表面,这在混合键合等应用中至关重要。 即使经过仔细的清洁/干燥,机械切割或激光烧蚀也会导致整个晶圆表面出现碎屑或颗粒污染物(可以使用ICOS™ F160XP 晶粒分拣和检测系统检测到)。
总结
综上所述,虽然传统的切割方法将继续成为许多应用的经济高效的解决方案,但在越来越多的情况下,等离子切割可以实现更高的成品率、灵活性和生产量,从而降低总拥有成本。 通过阅读我们的技术洞察文章或观看我们最近的SPTS网络研讨会,了解更多关于等离子切割的优势。
如果您想讨论自己的切割要求,以及了解SPTS等离子切割是否可以配合您当前的解决方案以解决任何问题,请与我们联系。
阅读《Chip Manufacturing 101》文章,了解更多关于半导体制造的基础知识,以及KLA的工艺控制和支持解决方案的工艺在制造供应链中发挥的关键作用。
如果您有兴趣加入我们共同实现未来技术的突破,并与我们一起推动人类进步,请浏览我们的人才招聘页面。
关注我们