The global automotive industry is in the early stages of a revolutionary shift away from internal combustion engines and an equally groundbreaking transformation in infotainment and advanced driver assistance systems (ADAS).
With these changes, today’s passenger and commercial vehicles are advancing from mechanical to electronic devices as cars and trucks become more electric, connected and autonomous. This is why the semiconductor industry’s role has never been more critical in moving the world forward with greener, smarter and more complex vehicles that meet automaker and driver requirements for performance, safety, improved navigation, communication and occupant comfort.
Automotive Semiconductors Demand a Zero-Defect Culture
Until recently, conventional motor vehicles have been equipped with only a few hundred semiconductors. By some accounts, 80% of innovation in automobiles happens with semiconductors, which are now the most foundational parts built into new cars.
Each electrical vehicle (EV), for example, can contain many thousands of chips. And, because of automotive industry requirements for safety and reliability, every chip must perform perfectly – every time.

Our industry’s challenge is to establish a zero-defect culture to meet strict standards for quality and reliability. New screening methodologies are required to identify all defects in all semiconductors. More than ever before, semiconductor manufacturing activity must be monitored to find all sources of potential reliability defects to meet quality goals – including those possibly missed by test – and latent reliability defects that may fail later in the harsh operating environment of the car.
Advantages and Challenges of Using Advancing Technologies
As consumer demand increases for more driver-assist features and high-quality automotive displays that look great and operate seamlessly for drivers and passengers, the need for chips based on the most advanced technologies available is increasing, including transistor designs as small as 5 nanometers. This brings new challenges for reliability since the technology hasn’t had much time to mature.
New materials like silicon carbide (SiC), for example, are essential to the electric vehicle segment. An EV’s inverter – which works like a transmission to convert electrical energy stored inside batteries into usable power in the vehicle’s electric motor to propel it – can be built using chips based on SiC to deliver greater power efficiency compared to well-established silicon (Si). Although SiC offers advantages over silicon, it’s expensive and much more difficult to work with, and as an industry, we need to focus on increasing the yield and avoiding excursions since starting costs for SiC wafers are 10 times that of silicon.
Focusing on Process Control and Advanced Screening
As automakers and their tier 1 suppliers increase vertical integration and invest more heavily in vehicle electronics capacity and process control to levels we’ve never seen, KLA is noticing increased interest from carmakers in the semiconductor industry. How will we continue to achieve the automotive quality requirements as automotive chip technology continues to evolve?
Process control is key to moving from research and development to ramping up high-volume manufacturing. KLA’s portfolio of process control solutions and specialized Si and SiC wafer processing solutions are supporting today’s evolution to a car that’s more electronic, efficient and reliable. Using machine learning technology, our I-PAT® automated inline screening solution evaluates each chip’s total defectivity during manufacturing. I-PAT (inline defect part average testing), which has been recommended by automotive standards for die-level screening to identify outliers, is being used to screen silicon chips used for infotainment and ADAS as well as both Si – and SiC-based power devices for use within an EV’s critical power inverters.
Chip Failure is not an Option
Whether equipped in EV drivetrains or safety and infotainment systems, failure in just one of the thousands of chips in today’s cars can cause breakdowns, resulting in an accident requiring costly repairs, injury or worse.
And that’s why KLA continues to help guide the industry to a zero-defect culture. Not only will the semiconductor industry benefit from improved yield – it will also keep us safer and reduce waste.
Global automakers are expected to sell 50 million EVs each year by 2030. Because these vehicles will have an increasing number of ADAS and infotainment features, we at KLA keep looking ahead to supporting development of technologies for greener, smarter cars that run safely and efficiently.
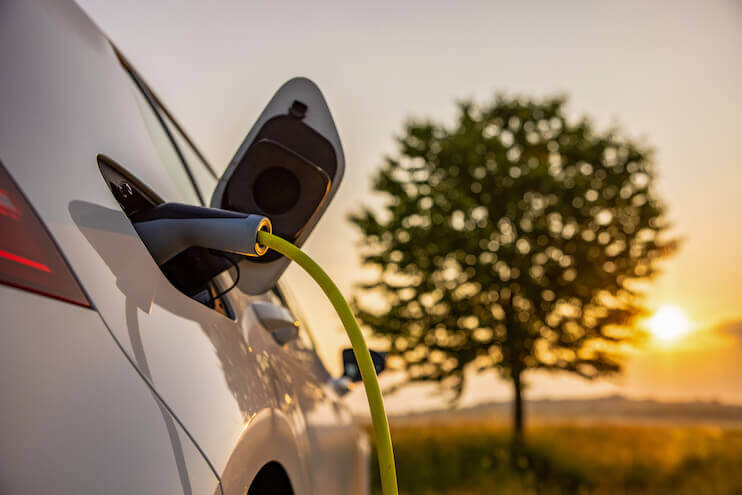
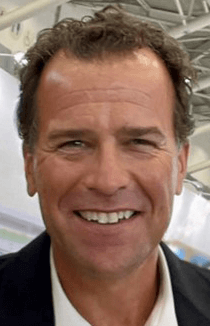
Dr. Chet Lenox is a KLA Fellow. Look for future leadership messages in KLA Advance’s Insights from our Innovators series.
Follow Us